Automatic sprinkler systems are one of the most important parts of a fire protection system. When a properly maintained sprinkler system is on site, the risk of someone dying in a fire is reduced by 50-75%, according to the Congressional Office of Compliance. It’s extremely important to ensure that automatic sprinklers are in working order to make sure that they are successful when needed.
Different types of sprinkler systems need to be inspected in different ways, but they should all be inspected at least once a year, however, some cities and states or insurance carriers require you to get your system inspected more often. Many sites choose or are required to conduct monthly inspections, quarterly inspections, and annual inspections as required by NFPA 25. In addition to the regular inspections, a fire sprinkler system should be inspected any time there is a change or modification to either the system or the building.
The Purpose
Fire sprinkler inspections are done to ensure a reasonable degree of protection for life and property from fire through regular inspection and testing methods as outlined within the NFPA standards. Inspection and testing should be performed by a properly trained and competent professional.The Inspection
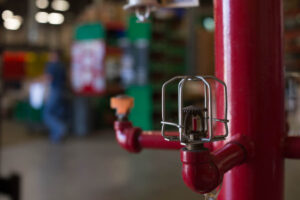
The Checklist
There are lots of pieces and parts, both electrical and mechanical, that can fail and cause a fire sprinkler system to not function properly, which is why inspection and testing is so important. All of these things need to be addressed during the inspection and testing process. The Monthly Inspection Inspect valves to verify that they are in the following condition:- In their normal open or closed position
- Properly sealed, locked, or supervised
- Accessible
- Free from external leaks
- Free of physical damage
- Appropriately labeled
- (Alarm Valves) Retarding chamber or alarm drains are not leaking
- Gauges shall be inspected monthly to ensure they are in good condition and that normal water supply pressure is being maintained.
- The gauge on the supply side of the dry pipe valve shall indicate that the normal supply water pressure is being maintained.
- The gauge on the quick-opening device, if provided, shall indicate the same pressure as the gauge on the system side of the dry pipe valve.
- Gauges on systems with low air or nitrogen pressure alarms shall be inspected monthly.
- Inspect water flow alarm and supervisory alarm devices for physical damage.
- Inspect and test the water flow alarm by opening the test connection on a wet pipe system and the bypass connection on a dry pipe system.
- If the sprinkler system is hydraulic, inspect the hydraulic nameplate to ensure that it’s attached and easily seen.
- Inspect fire department connections to make sure they are visible and undamaged, and ensure that gaskets and valves are not leaking or damaged.
- Inspect pressure reducing valves and relief valves, if provided, to verify the following:
- In the open position
- Not leaking
- Maintaining downstream pressures in accordance with the design criteria
- In good condition, with hand-wheels installed and unbroken.
- Inspect all sprinkler heads, including the piping and fittings.
- Ensure that there are extra sprinkler heads on site, as well as the tools, to change out the sprinkler heads.
- Interior of dry pipe valves
- Conduct a main drain water flow test to determine whether there has been a change in the condition of the water supply piping. (This test is required to be conducted quarterly if the water is supplied through a backflow preventer and/or pressure-reducing valve.)